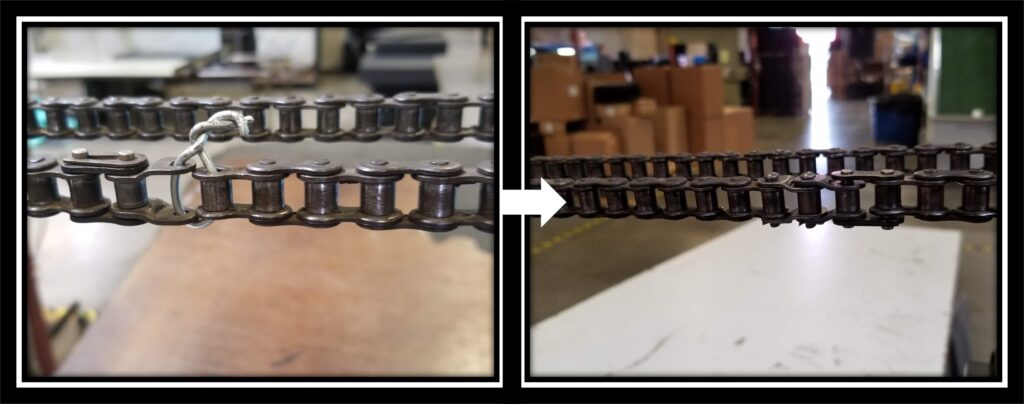
The Foam Shop
Giant Drone Foam Case:
Challenges: Customer wants specific material due to mechanical properties preference. That Foam cell material only came in 4′ x 8′
Action Plan: Determined best cross-section that can be nested, and set-up manufacturing plan for operators to team-up and produce.
Conclusion: Created 4 sections that can get maximum material yield and still retain structure integrity. Additionally, created keys to support assembly process and avoid using wrong parts.
Pankl Aerospace:
Challenges: Customer has 5 different shafts that are used for helicopters, and wanted all to fit in one case. Also, wanted it to be low cost.
Action Plan: Used customer provided 3D model, and utilized AutoCad to lay them side by side and found common Diameters. Doing so, I was able to categorize 2 groups. So the focus was to make it multipurpose for 2 groups.
Conclusion: To keep the price low cost, minimal materials were used. To compensate for 2 groups, sliding mechanism was improvised to accommodate 5 different shafts.
All others projects:
This is to give you an idea what my day to day basis was like. Making Customers ideas into life. Designing and Manufacturing from initial to final.