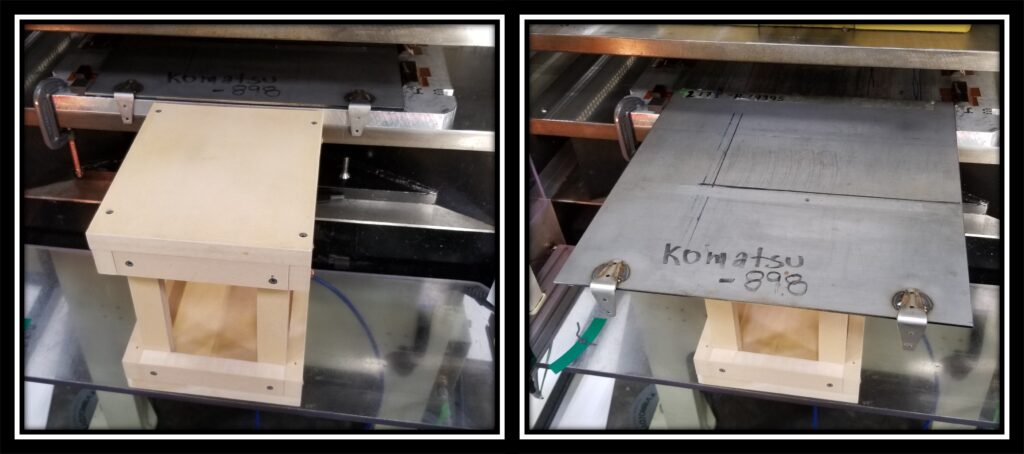
The box was a simple and quick build with a low friction material on top, which allows for Steel Plate to slide on.
Operator is no longer having to carry the Steel Plate, instead, let it rests.
“Identify the pain point and eliminate it! When operators are happy, exceptional products are inevitable.” – Daniel Diaz
Fralock
Automating Peel, Tensile & Elongation Testing process:
Situation: The business was picking up, and customers were ordering more Adhesive Tapes. Most of these customers are DoD contractor and requires the process to follow standards per spec. Normally these would get outsourced to ensure we are complying.
Challenge: The vendor was increasing the cost, and it was no longer profitable. On the other hand, Fralock has the capability to perform testing in-house, but was not in compliance. We needed to develop and establish the process of Peel, Tensile & Elongation, and Electrical Resistance to win the business.
Action Plan: Establish a process to ensure compliance with ASTM D1000 for Peel Testing and Tensile & Elongation testing, and ASTM D3330 for another Peel Testing. Delegated task for STD-200 for Electrical Resistance. With this opportunity, I was able to automate the process that guides operator step by step on what to do depending on Testing selected, and the report generated depending on the inputs from operator and testing. The process was designed and implemented with ease of usage in mind.
Conclusion: Fralock officially added a new capability in the arsenal, we were able to manufacture and comply to specs. Also, the MTS Test Suite equipment was no longer under-utilized.
Lawrence Livermore:
Situation: Customer wanted to laminate Kapton on both side of the metal coil due to mechanical properties preference.
Challenges: We didn’t have the capability to manufacture due to limitation of size and weight of the coil. Several attempts had been made to test cut a sample, but the quality wasn’t on par due to not being able to control the weight and size of the coil. This was a high risk for injury and defects if not handled properly. Not last but least, the deadline was coming up quickly
Action Plan: Design and manufacture fixture to create extended cores and roll stands. Determined resources that are available, and finding the right people that can support. Set up a process to enable an Operator the ability to unwind the coil onto the table and perform CNC Knife Cutting operation. Then rewind the coil upon completion to allow for the next operation.
Conclusion: These extended reels and stands were used to support manufacturing the products within the processes of Lamination, CNC cutting, Inspection, and Packaging. As a result, I was able to mitigate risk of injury, quality defects, maintained low cost and on time delivery.
R&D for Facebook Reality Lab:
Situation: Customer needed to manufacture Microfluidic Flexible Interconnected cable for their VR application in their next tradeshow. Other Vendors including Facebook did not have any success of manufacturing Microfluidic Cables.
Challenges: To ensure edge quality, such as burrs, burnt edges, and integrity of the walls between channels.
Action Plan: Conducted design of experiment and set-up parameters to understand machine capability. This was to determine maximum number of channels and thinnest we can manufacture while maintaining quality. Several Method of manufacturing was done in parallel.
Conclusion: Optimal method has been established. We were able to identify the thinnest the channels can be, and minimum width of a wall can be to maintain integrity. The customer performed a destructive testing and was able to withstand high temperature and pressure.
R&D for Lam Research:
Situation: This product, Special O-ring, goes inside wafer-making machine. The customer was using a material that was consumed rather quickly and was looking for alternative materials that would last a long time and can handle plasma. They’ve come to us to use our special material, Cirlex.
Challenges: We didn’t have capability to manufacture specific features this customer was looking for. There was no tooling available to do the lay-ups properly as it was not a standard process. Additionally, Autoclave process was not designed to holed tight tolerances between features.
Action Plan: Gather the team and collaborated on the drawing board. We’ve narrowed down to using 5 Black Cirlex Sheets and 3 brown Kapton sheets that needed to be placed into Autoclave and Laminate to create the converted raw material shown in first image. Designed Fixture to make it easy for Autoclave to do Lay-ups. To ensure the shaft is able to slide through the hole, thermoforming process was developed using custom fixture and tooling to accurately press and form the holes. The idea was to allow shaft to slide thru and still maintain pressure/liquid and hold tight tolerance.
Conclusion: I’ve determined the feasibility of manufacturing the parts. The process for BOMs and Routing have been established and documented.
New Product Implementation for Lam Research:
Situation: These Heat Shields were used to protect operator for when they are inside of the wafer making machine. Lam was in process of releasing a new prototype of a wafer making machine and needed a vendor that can manufacture a prototype quickly. Lam came to Fralock as no one else was able to promise a delivery as quickly.
Challenges: We didn’t have the capability to cut 1/2″ thick foam laminate with silicone rubber, and to fabricate sheet metals.
Action Plan: Provided engineered solutions, negotiated with the customer on what we can do, redlined the drawing to reflect the process we were capable of, worked with a vendor who fabricated sheet metals for us, and purchased tooling set for CNC Knife Cutting machine. Developed a parallel process so that we are not waiting on the fabricated sheet metals. Also, established a process the ensure operator can manufacture and assemble the components.
Conclusion: I’ve determined the process and established the BOMs and routings. I’ve produced and manufactured from prototyping, First Article Releases, to Production Releases. This has opened up new business of Fralock doing multiple configurations of Heat Shields.
R&D Projects:
Just to show a few, these projects required time and patience. Determining which materials and parameters work best. There are some “failures” or is it? Perhaps, we all learn what can go wrong! Thus improving quality and knowledge of manufacturability.